Plating
Zinc electroplating offers corrosion resistance by acting as a protective barrier and sacrificial coating. As zinc is more reactive than steel, it corrodes first, safeguarding the steel substrate. The corrosion rate of zinc is significantly slower than that of steel, allowing a thin zinc coating to provide long-term protection.
Electroplating Process:
The electroplating process begins with thorough cleaning of the fastener surface using alkaline detergent solutions. Acid treatment follows to remove rust or surface scales. Ensuring cleanliness is crucial to enable proper adhesion of the coating to the metal surface.
Electroplating is accomplished through electro deposition. Fasteners are immersed in a chemical bath with dissolved zinc. When a direct current is applied, the zinc metal at the anode dissolves, and the resulting metal ions migrate to the cathode, forming a thin coating on the fastener. The thickness of the zinc plating depends on factors such as plating bath duration, electric current, and chemical composition.
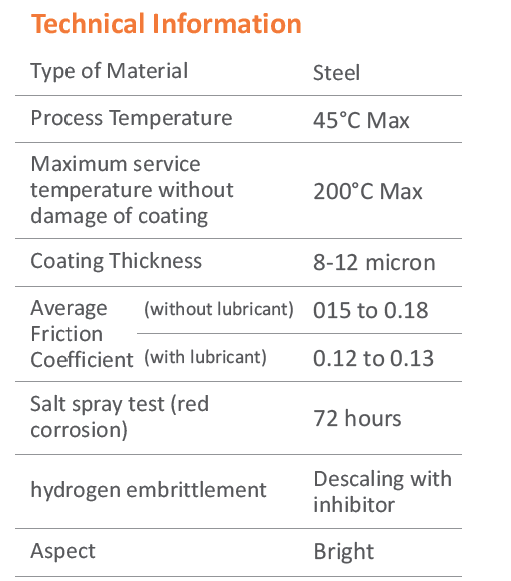
Advantages:
Electroplating provides a smooth, shiny, and drip-free surface, which is desirable for aesthetic reasons. The thin coating does not interfere with fastener threads. Additionally, electroplating is a cost-effective option.
Hydrogen Embrittlement:
During acid cleaning and the electroplating process, atomic hydrogen is generated and can penetrate the steel, leading to embrittlement of the fastener structure. The electroplated coating traps hydrogen within the fasteners, which can migrate to areas of high stress, causing microcracks and eventually resulting in brittle failure. To mitigate this, fasteners need to be baked soon after plating to drive out the trapped hydrogen. High-strength fasteners are particularly susceptible to hydrogen embrittlement, as greater strength or hardness increases the risk of hydrogen-induced failure.
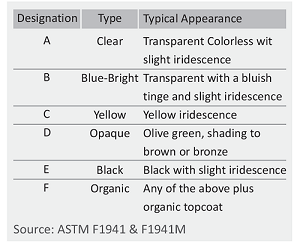
At Hanwant Auto Tech, we have a Fully Automatic Electroplating line with synchronized Auto loading system and a hydrogen De-Embrittlement furnace for post-plating de-embrittlement baking. This streamlined process ensures the highest quality plating without any wasted time in-between.
Passivation: Passivation involves applying a light coat of material, such as metal oxide, to create a protective barrier against corrosion from environmental factors like air and water. It strengthens and preserves the appearance of metal.
Chromate Conversion Coatings: In more challenging environments, fasteners can undergo chromate-conversion coating for additional corrosion protection. Grade 5 or Class 8.8 fasteners typically use clear or blue-bright trivalent chromates (designated A or B), while Grade 8 or Class 10.9 fasteners are supplied with hexavalent-free yellow chromate C3+.
Hanwant Auto Tech is ISO 9001 and TS 16949 certified, ensuring strict quality standards. We take various precautions to ensure our fasteners meet or exceed governing specifications, and full traceability to the original manufacturing lot number is available.
Hot Dip Galvanizing (HDG)
Hot-dip galvanizing (HDG) is a widely used method to protect steel fasteners from corrosion. The HDG coating is low maintenance and offers exceptional corrosion protection for steel structures, lasting 50-70 years in various atmospheric environments, including industrial, urban, marine, and rural settings.
HDG provides two forms of corrosion protection: barrier and galvanic (cathodic). It serves as a semi-impermeable barrier, shielding steel from environmental elements that trigger corrosion.
Zinc galvanizing provides effective protection for steel due to zinc’s higher reactivity compared to steel. The zinc coating sacrificially corrodes, safeguarding the steel substrate. Zinc corrodes at least 10 times slower than steel, allowing a thin zinc coating to provide long-term protection.
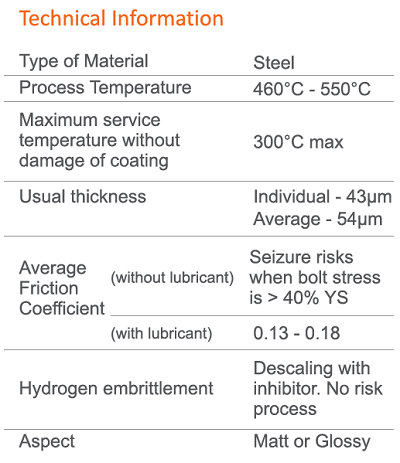
The hot-dip galvanizing process begins with meticulous cleaning of the fastener surface to remove organic contaminants like dirt, grease, or oil. Scale and rust are eliminated through pickling using heated sulfuric acid or ambient temperature hydrochloric acid solution. After cleaning, the fasteners undergo a thorough water rinse.
Next, the parts are immersed in a flux tank containing an aqueous solution of zinc ammonium chloride. The fluxing process removes oxides from the steel surface and prevents further oxide formation prior to galvanizing. It also facilitates the bonding of zinc to the steel surface.

In the galvanizing phase, the fasteners are fully immersed in a molten bath of at least 98% pure zinc, heated to a temperature ranging from 460°C to 525°C. After slowly withdrawing the parts from the zinc bath to remove excess zinc, they are cooled either by air or water to solidify the coating and make them ready for handling.
The final step involves thorough inspection. Hanwant Auto Tech production facilities are certified with ISO 9001, ISO/TS 16949, ISO 14001, and BS OHSAS 18001. We take multiple precautions to ensure that our fasteners meet or surpass the required specifications. Additionally, full traceability to the original manufacturing lot number is provided.