Heat Treatment
Heat Treatment of Carbon Steels and Carbon Alloy Steels:
Heat treatment is a crucial process for improving the mechanical properties of carbon steels and carbon alloy steels, specifically their tensile and yield strength. This is achieved by modifying the molecular structure of the steel to create a more robust microstructure. The structure of steel comprises two key factors:
- Grain Structure: Referring to the arrangement of atoms in the metal.
- Grain Size: Denoting the size of individual metal crystals. Larger grain sizes are generally associated with lower strength, hardness, and ductility.
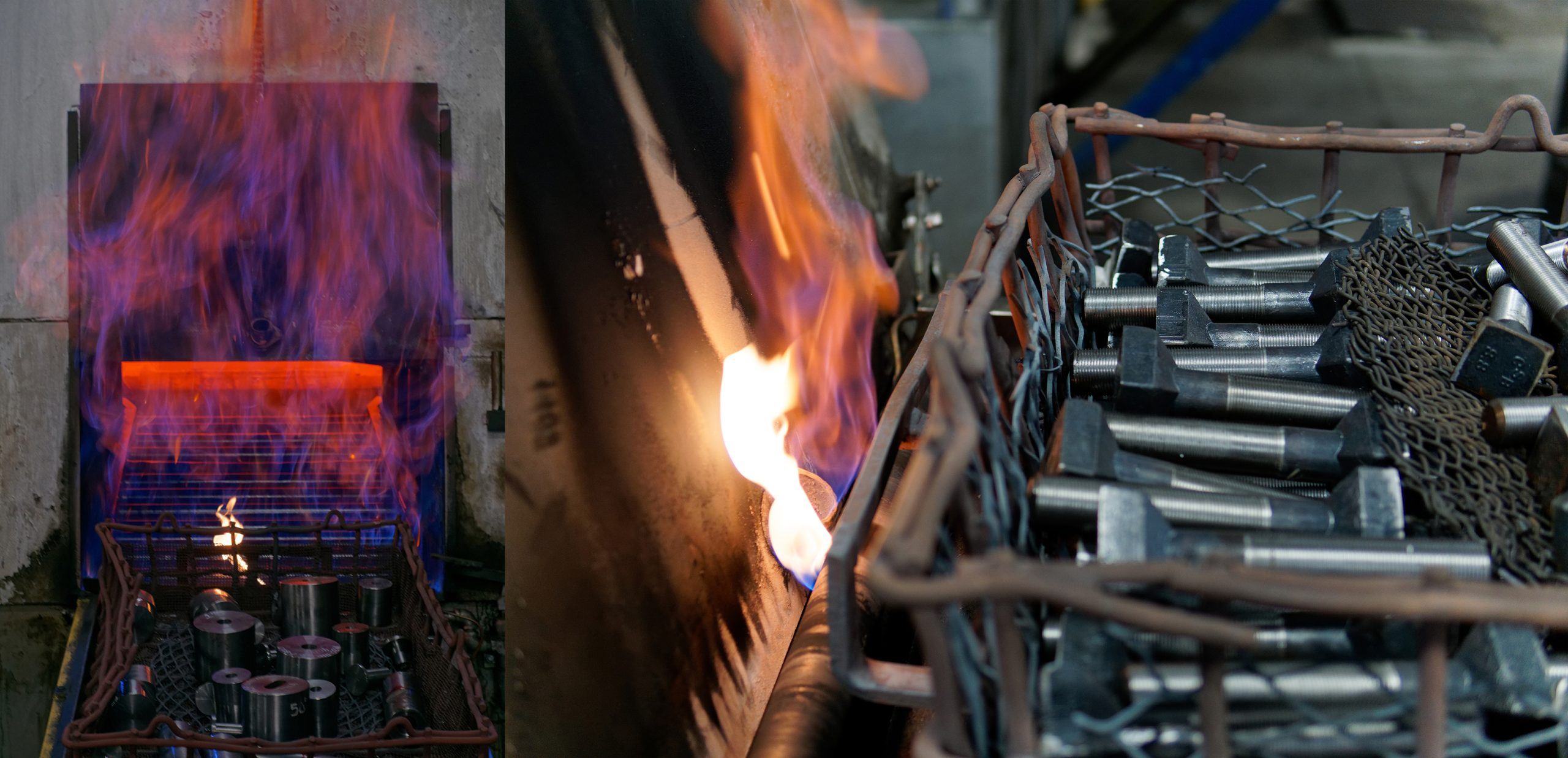
During the alloying process, elements like carbon are introduced to the metal, which disrupts the flow of individual grains, thereby enhancing strength. Hence, controlling the crystal structure of the metal is essential for successful heat treatment.
Metals can exist in various phases, such as ferrite, austenite, and cementite. To comprehend these phases, we can refer to the Iron-Carbon Phase Diagram. The Y-axis represents temperature, while the X-axis represents the carbon content of the steel. The leftmost side of the X-axis represents the ferrite phase (low carbon content), whereas the rightmost side represents the cementite phase (high carbon content), also known as iron carbide. The curved line above 1333 ºF represents the austenite phase of steel.
At room temperature, ferrite (low carbon steel) possesses a body-centered cubic structure that can only absorb a minimal amount of carbon. Due to this limitation, any excess carbon separates from the structure to form carbides, which combine to create small packets of a highly rigid crystal structure within the ferrite called cementite. However, when ferrite is heated above the transformation line (austenite line), its structure changes to face-centered cubic, enabling carbon absorption into the crystal structure.
Upon entering the austenitic phase, all the cementite in the steel dissolves into austenite. If the steel is slowly cooled, the carbon separates out of the ferrite, causing a reversion from face-centered cubic back to body-centered cubic structure. Cementite islands then reform within the ferrite, resulting in the steel retaining its original properties. However, rapid cooling or quenching of the steel in a quenching medium like oil, water, or cold air prevents carbon from exiting the ferrite’s cubic structure, thus trapping it. This leads to the formation of a martensitic microstructure, which imparts highly desirable mechanical properties to steel fasteners.
During quenching, it is challenging to achieve uniform cooling throughout the specimen. The surface cools faster than the interior, causing the austenite transformation to occur over a range of temperatures. As a result, the material can exhibit variations in microstructure and properties depending on its position within the material.
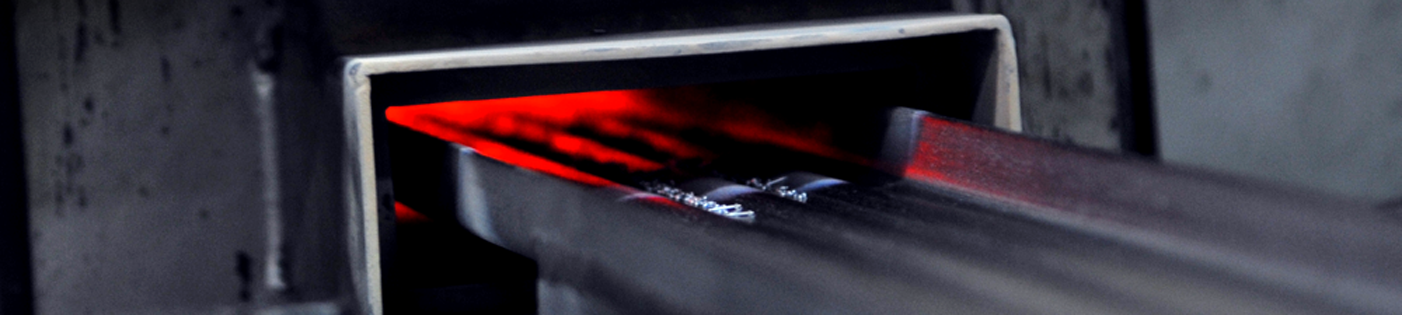
Types of Heat Treatment Processes:
- Normalizing: This process is used for ferrous metals to eliminate internal stresses caused by welding, machining, and heat treating. It results in the formation of bainite, martensite, and pearlite, making the steel harder.
- Aging: Also known as precipitation hardening, this method involves processes like solution heat treating and precipitation heat treating. It enhances the mechanical properties of alloys such as maraging steel, Waspaloy, and Uranium alloy.
- Annealing: The purpose of annealing is to soften materials. The metal is heated to its critical temperature and then slowly cooled, increasing electrical conductivity and allowing for recrystallization. Different types of annealing methods include recrystallization annealing, partial annealing, and final annealing.
- Tempering: Metal is heated below its critical temperature range (205ºC to 595ºC), with techniques like Austempering and Martempering. The quality of steel is determined by the tempering colors observed.
- Decarburization: This process involves heating a metal below 1740ºF and exposing it to surroundings rich in carbon. It hardens the metal surface and increases its strength.
- Stress Relieving: Metal is heated below its critical temperature to quickly and efficiently remove internal stresses. Commonly used for boilers, air tanks, and pressure vessels.
- Quenching: Also known as hardening, the metal is heated above its critical temperature and then rapidly cooled. It results in increased hardness, but the metal may become brittle. Tempering is often performed to address this issue.
- Case Hardening: Also referred to as surface hardening, this process is used to produce hardened surfaces for components like firing pins, drilling screws, and engine camshafts.
- Cryogenic Treatment: Metal is subjected to extremely low temperatures below -190ºC to remove internal stresses and enhance resistance. This process improves thermal and electrical properties and includes methods such as cryogenic machining, cryogenic hardening, cryogenic rolling, cryogenic deflashing, and cryogenic deburring.